Located in Sandy, Utah, (near Salt Lake City), DeltaValve is a world leader in the design, engineering, and manufacturing of critical service equipment for delayed coking. Our renowned fully automated coke drum unheading valves have become a global standard for safe, reliable, and easy-to-operate coke drum unheading.Available for both bottom and top coke drum unheading, our valves create a totally enclosed system from the top of the coke drum through to the coke pit, isolating personnel and equipment from coke-drum fallout and other hazards associated with the unheading process.Another recent innovation from DeltaValve is our retractable center-feed injection device. This device combines the benefits of utilizing fully automated coke drum bottom unheading valves with the benefits of traditional coke drum center-feed injection. Center feed injection creates flow channeling up the center of the coke drum, allowing for even and consistent heating/cooling of the coke drum, and reducing significant coke drum stresses and top head eruptions typically associated with side feed entry.Other DeltaValve equipment for the delayed coker include a full range of in-line repairable isolation valves, complete hydraulics and controls systems, auto-switch coke boring/cutting tools and enclosures, top head blowout diverters, and more.
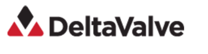
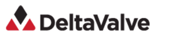
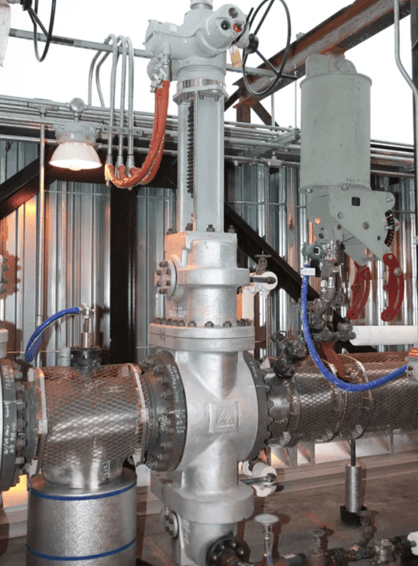
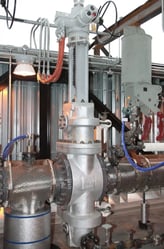
Physical/Technical Attributes
GV850 Isolation Valve
Design ASME B16.32
Construction Cast
Metallurgy SA217 GrC12, C5, WC9, WCC, WCB
Seat Style Dual live-loaded, metal
Actuation Hydraulic or electric
Shut-off Double block and purge with 100%
verifiable positive isolation
Positive Lockout Removable lock-out pin
End Connection ANSI B16.10 300#, 600#, 900# RF, RTJ
Valve Size6 - 36 inch
Purge MediaSteam
Function On/off, throttling
Application Photos
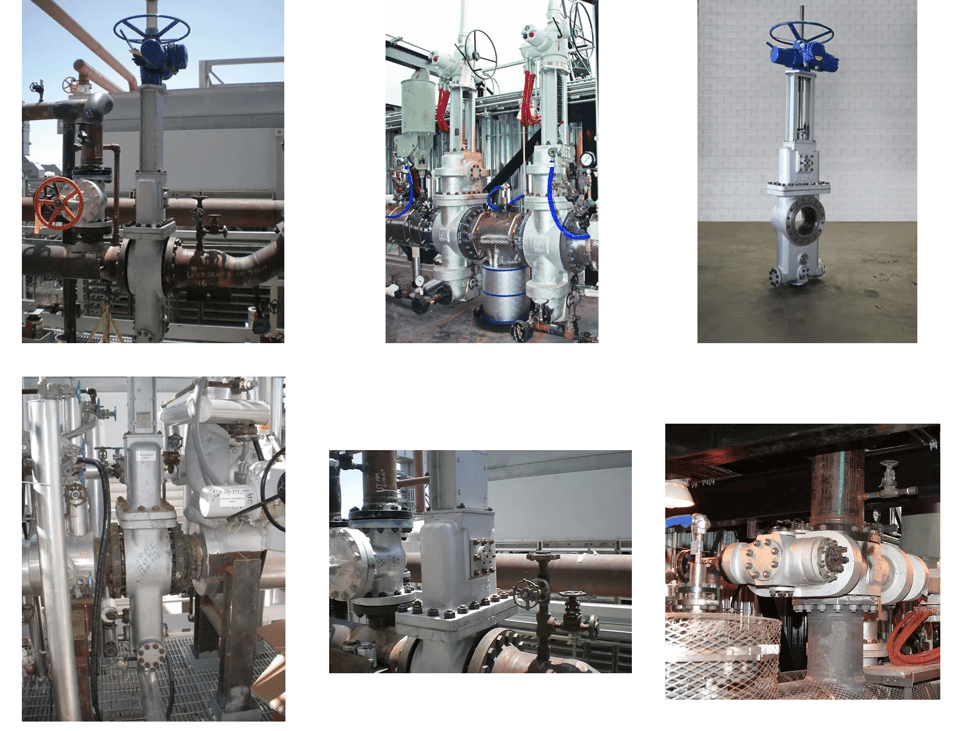

In-line Repairable Isolation Valves
For DCU Service
DeltaValve’s isolation valves are reliable, low maintenance, tight shut-off isolation valves, designed for high temperatures and harsh applications. The throttling version is capable of operating continuously in the partially open (throttled) position while isolating the body internals from the process. Steam purge requirements for our isolation valves are extremely low. The innovative valve design provides practical and efficient in-line maintenance of all internal components without removing the valve body from the line.
Key Advantages
Proven technology
Low maintenance
Tight shut-off
Steam purged
In-line maintenance
Reliable design
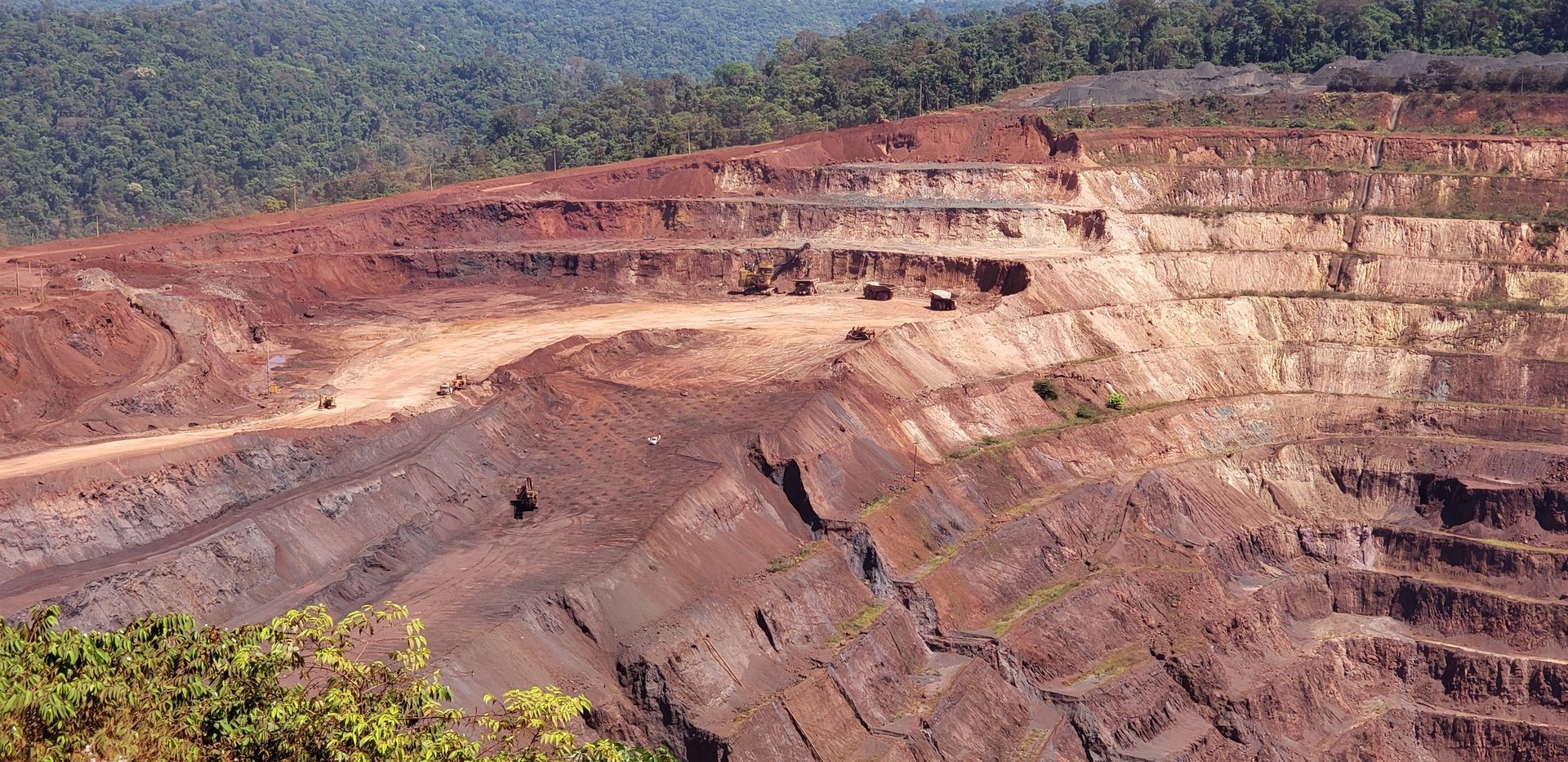
Links
The logo in this website are trademarks copyrights owned by Strauss Tech LLC. Copyright © 2020 Strauss TechLLC. All rights reserved. - Terms & Conditions - Sitemap
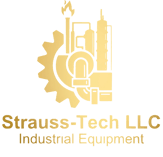

Contact Information
1330 N State Street, Provo, Utah 84604. Phone: (801) 941-1210